Mobile robots are becoming more commonplace in industry. Most robots are reliant upon advanced anti-collision and navigation systems, which can often be computationally demanding, costly, and difficult to maneuver.
This article explains how strategically positioned range sensors can provide an adaptable, compact, and inexpensive alternative, proving that it can be easy to utilize this technology.
Automation enhances the consistency, quality, productivity, and safety of industrial processes and since the early 1900s, the role of automation in industry has been increasing. Automation has changed from machines that performed easy and repetitive tasks to industrial robots that gather information and react to the environment around them.
Reliable Navigation Systems are Essential for Safe, Efficient Mobile Robots
Industrial robots are no longer stationary. Now mobile, robots can be utilized in an entirely new set of applications. Tasks that have traditionally been performed by humans or human-operated vehicles are now being completed by robots, for example, the collection of goods and the transportation of goods around warehouses.
Industrial mobile robots must have the ability to navigate increasingly complex and constantly changing environments efficiently and safely.
They must be able to perceive obstacles in front of them and make instant decisions about how to avoid them to achieve this.
A pizza delivery colleague who regularly crashes or drives around the neighborhood aimlessly before delivering a cold pizza would not be desirable. Similarly, people want mobile robots to efficiently complete their tasks without collisions.
Sensors Help Robots ‘See’ their Environment
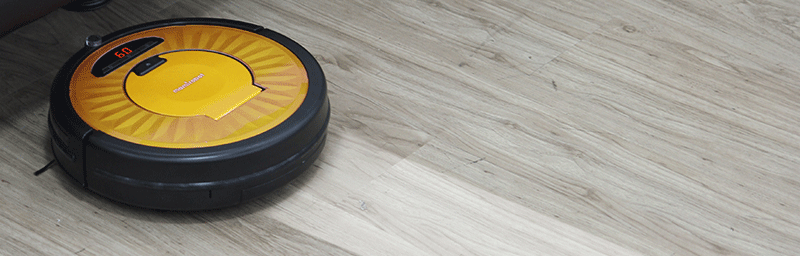
Collision-based technology, where robots distinguish objects by bumping into them, is the easiest solution for robot navigation. The robot can then adjust its direction to miss the obstacle.
This low-tech solution may be appropriate for basic and compact robots, for example, robot vacuums, but is not likely to be the most effective choice for robotic forklifts traveling around expensive goods and people.
Ultrasonic sensors emit sound waves and detect waves that return to the sensor after being reflected by the obstacles.
Ultrasonic sensors can communicate the presence of an obstacle to the robot, but the essence of ultrasonic sensors means that their operation is somewhat restricted and prone to error. Their update rates are slow and their maximum range is frequently short.
LiDAR Laser Scanners Provide Precise Positioning – At a Cost
LiDAR (Light Detection and Ranging) laser scanners provide a high-tech solution for robot anti-collision. They function on the Time-of-Flight principle, where light generated from the scanner reflects from obstacles in front of the robot and returns to the sensor.
The length of time that the light takes to travel from the source to the object and back to the detector is utilized to compute the distance between the object and the robot.
Rotating LiDAR systems use a rotating mirror to divert the laser beams to analyze their complete environment. Laser scanners offer instant and accurate maps of a robot’s surroundings, allowing for precise anti-collision and obstacle avoidance even in changeable situations. However, laser scanners are often costly and deliver thousands of data points each second, creating an excess of data that requires extensive processing power to evaluate.
This implies an expensive system that utilizes a high amount of energy. Laser light can harm human eyes. Therefore, laser scanners must adhere to strict safety regulations.
Thoughtfully Placed ToF Distance Sensors Can Provide Coverage at a Fraction of the Price
It is possible to produce a “selective point cloud” using strategically placed distance sensors to bring a more compact and inexpensive solution compared to traditional environment-scanning ToF technology.
This can also be complementary to full environment-scanning and provide redundancy at a fraction of the price.
Mobile robots can observe their environment and perform anti-collision employing a few single-point distance sensors with the correct sensor configuration. This greatly reduces cost and simplifies the system compared to the modeling and interpretation of their entire 3D environment.
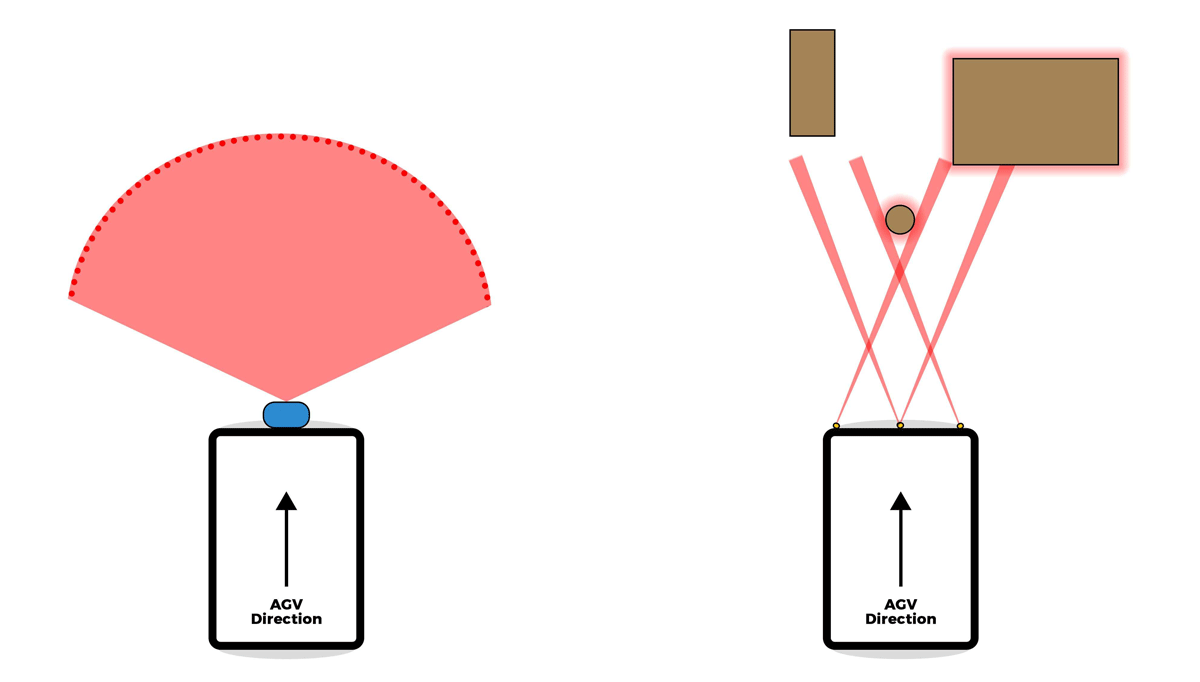
Figure 1. Left: Anti-collision system using a laser scanner, right: example of object detection using Terabee sensor arrays.
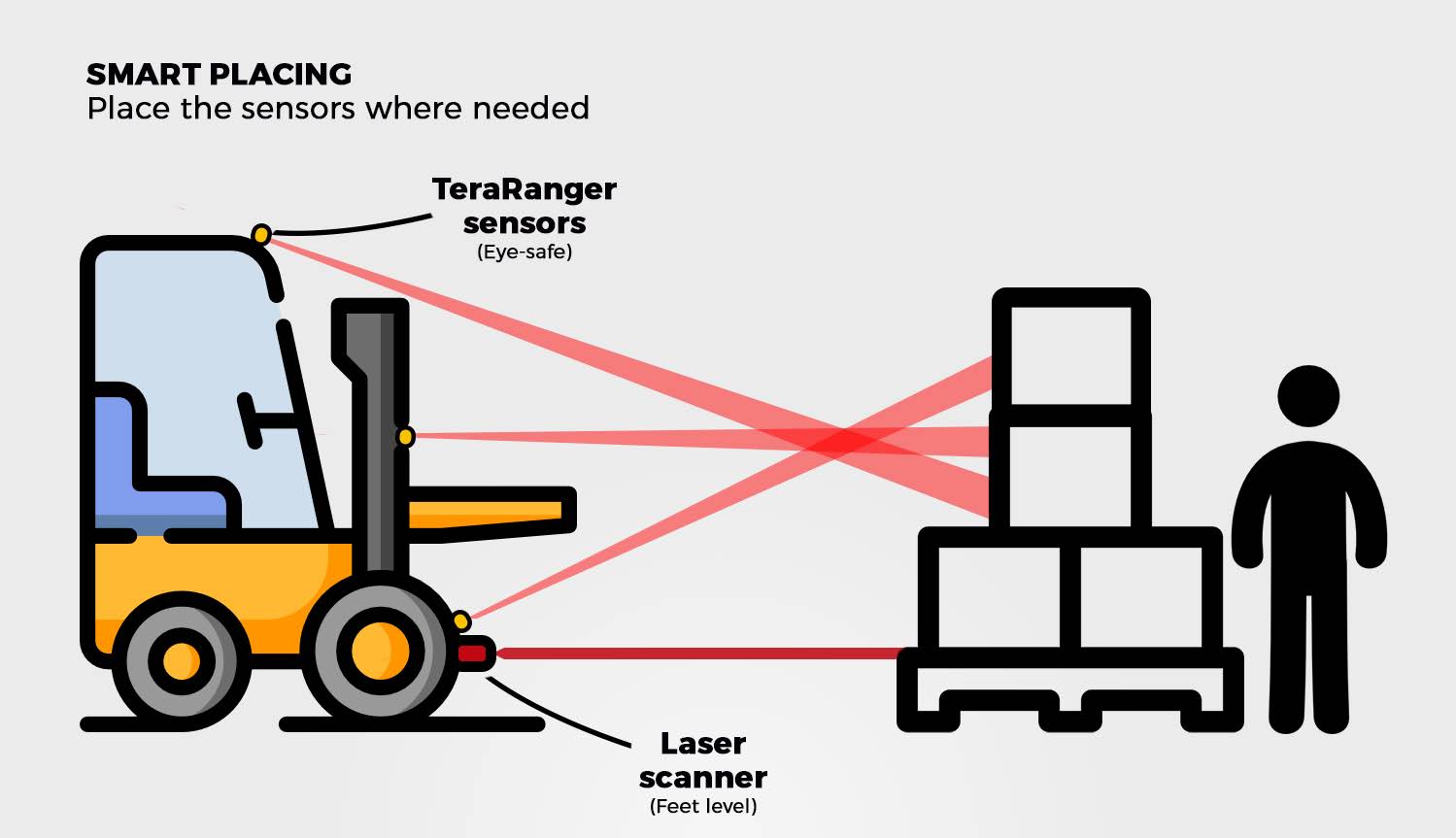
Figure 2. Complimentary technology, overcoming bi-dimensional limitations.